ERP Projects are among the most challenging and expensive solutions to implement and successfully integrate into an organization. A well planned and executed ERP project should increase organizational productivity and efficiency. There are many success stories attributed to successful ERP projects. However, the headlines regarding ERP systems are frequently dominated by stories of ERP implementations gone wrong and negatively impacting a business and its customers.
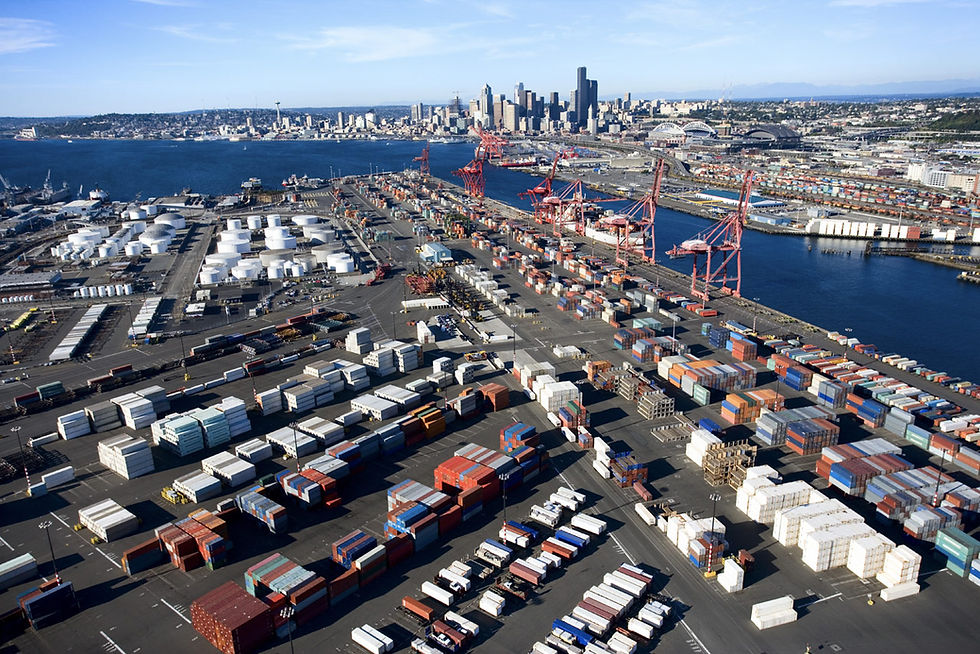
While many factors contribute to the success or failure of an ERP Project, process issues are often one of the most frequent complaints voiced by project sponsors and those tasked with working with the new system. To highlight the significance of this potential problem, imagine the sales staff on the front line of a business not being easily able to take and process customer orders after an ERP project goes live. In 2013, that is exactly what happened at Avon, leading to the write down of an estimated $125-million-dollar ERP project. After going live with an ERP project, the company experienced significant issues in a number of areas including impact to their agent’s ability to log in, reserve inventory or save orders [1].
So how can you avoid creating a major a mess and driving your employees, suppliers and customers away after you implement your ERP project?
Many organizations make the mistake of viewing an ERP as only a technology project and not an organizational transformation project with many touch-points.
ERP systems and software come in many shapes and sizes from vendors including SAP, Oracle, Workday, Infor, Microsoft and many more. There are many drivers as to why an organization may consider an ERP project, including process improvement, standardization of business processes, enforcement of financial compliance and controls, automation of manufacturing or distribution or consolidation of many different systems.
The foundation for many ERP systems are core business processes. ERP projects often involve changes in the way that users such as executive management, employees, customers, vendors and suppliers conduct business leveraging these processes.
To help ensure success many different organizational areas should be involved in the project from start to finish, including planning, testing and training of any process based actions and activities that are impacted or leverage the ERP system. This also often means including the people that actually work with the processes encompassed by the project, not just an isolated project team.
There are several fundamental actions that an organization implementing a new ERP system or modifying and existing ERP can follow to ensure they have accounted for all key processes and planned for both the impact of any change after their project goes live.
Document existing processes. Think in terms of both regular processes, but also those that occur infrequently.
Document any new processes. Many vendors can provide a functional list, but take the time to walk through and see them in person.
Compare your existing processes to the new processes. Look for missing, different and similar processes. For different processes you may want to explore if a new process makes sense from a best practices or efficiency standpoint.
Create a plan for how new processes or missing processes will be addressed. Paying careful attention to what is going to change, how and who this impacts.
Prior to going live complete a check point to make certain there are no unaccounted processes.
These actions can often be facilitated by some great process mapping and management tools designed just for this purpose.
With some process focused up front planning and inclusion of those organizational areas and people impacted by any changes, it is possible to have a successful ERP project that provides all the benefits promised and have everything run smoothly afterward.
References and Citations:
http://www.informationweek.com/software/information-management/inside-avons-failed-order-management-project/d/d-id/1113100
Disclaimer, Copyright and Trademark Statement
This article is provided for informational and educational purposes. It makes no warranties as to the claims, accuracy or fitness of information provided, referenced or cited. Use of the information, instructions and any examples contained in this work is at your own risk. There should be no implied endorsement of this article by any person or organization referenced.
All trademarks, company, product and services names, images, descriptions, or public website content are property of their respective owner as source referenced. It is your responsibility to ensure that your use thereof complies with such licenses and/or rights.